Landscape garden decorative resin animal statue
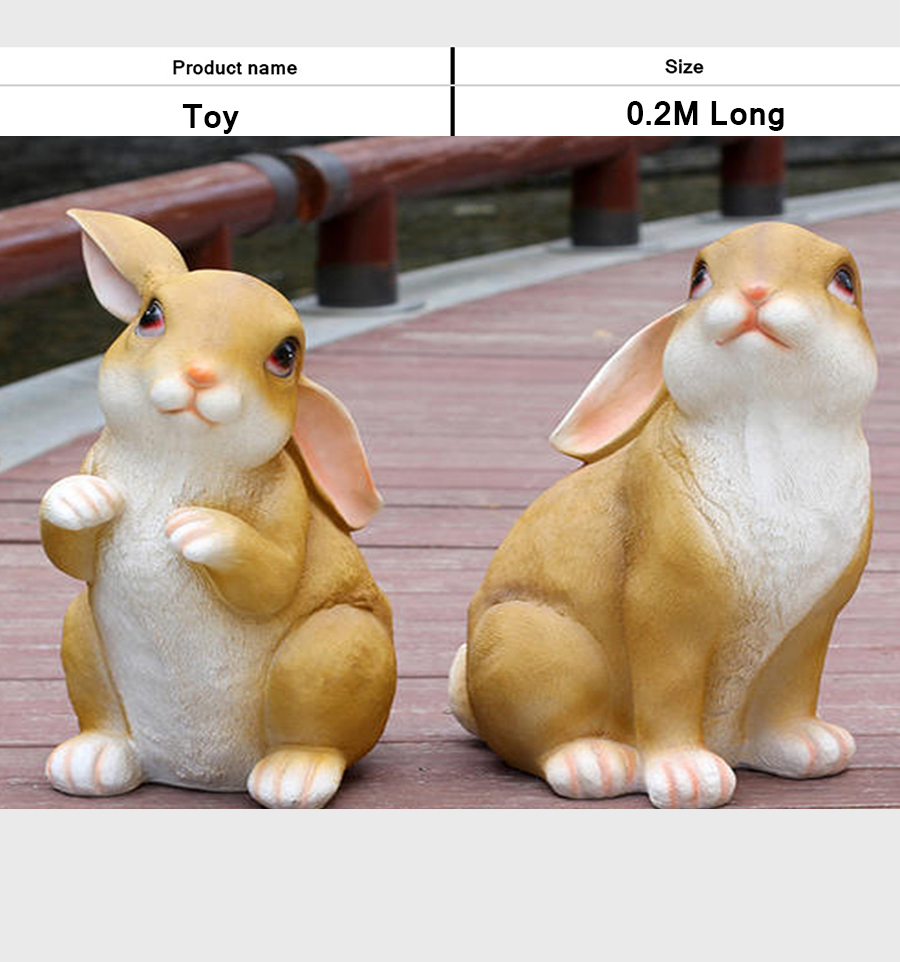
MORE INFORMATION
Input |
AC 110/220V ,50-60HZ |
Plug |
Euro plug / British Standard / SAA / C-UL / or depends on request |
Control mode |
Automatic / Infrared / remote / coin / Button / Voice / Touch / Temperature / shooting etc |
Waterproofing grade |
IP66 |
Working condition |
Sunshine, rain, seaside, 0~50℃(32℉~82℉) |
Optional function |
Sound can be increased to 128 kinds Smoke,/ water. / bleed / smell / change color / change lights / LED screen etc
interactive(Location tracking) / conversine(currently only Chinese) |
AFTER-SALE SERVICE
Service |
Need be cut for shipping,fwill provide a detailed installation manual. |
Warranty |
We provide 2 years warranty for all of our antrimatronic models, the warranty pieriod starts
from freight arrives at destination port. Our warranty covers motor, reducer, control box, etc. |

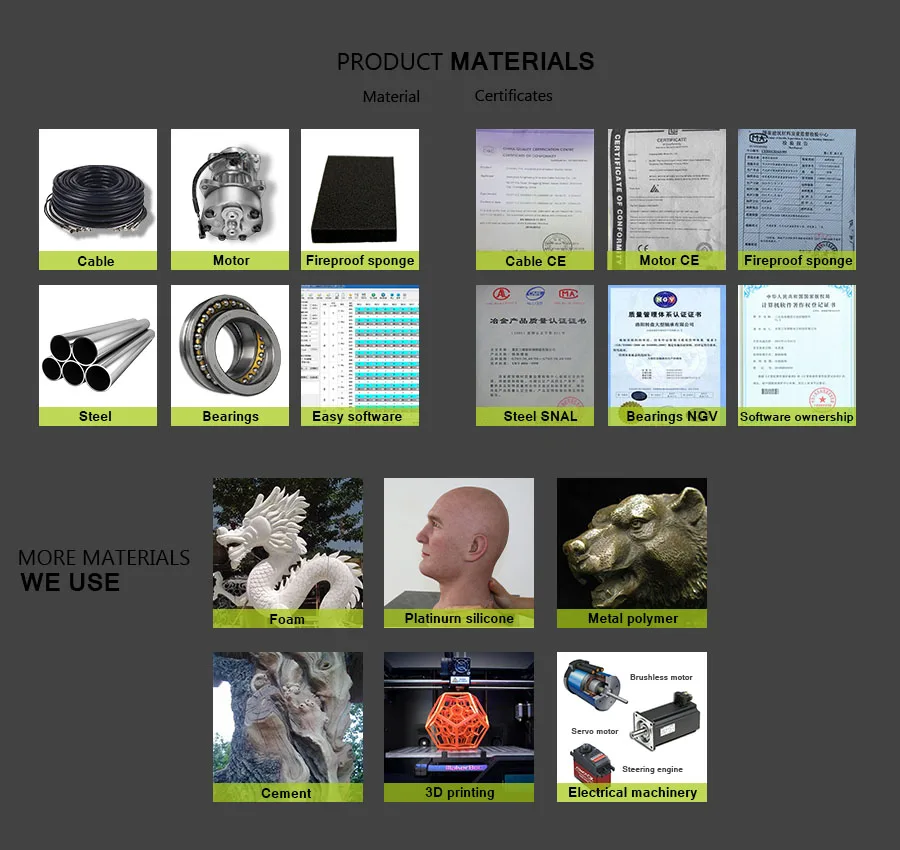
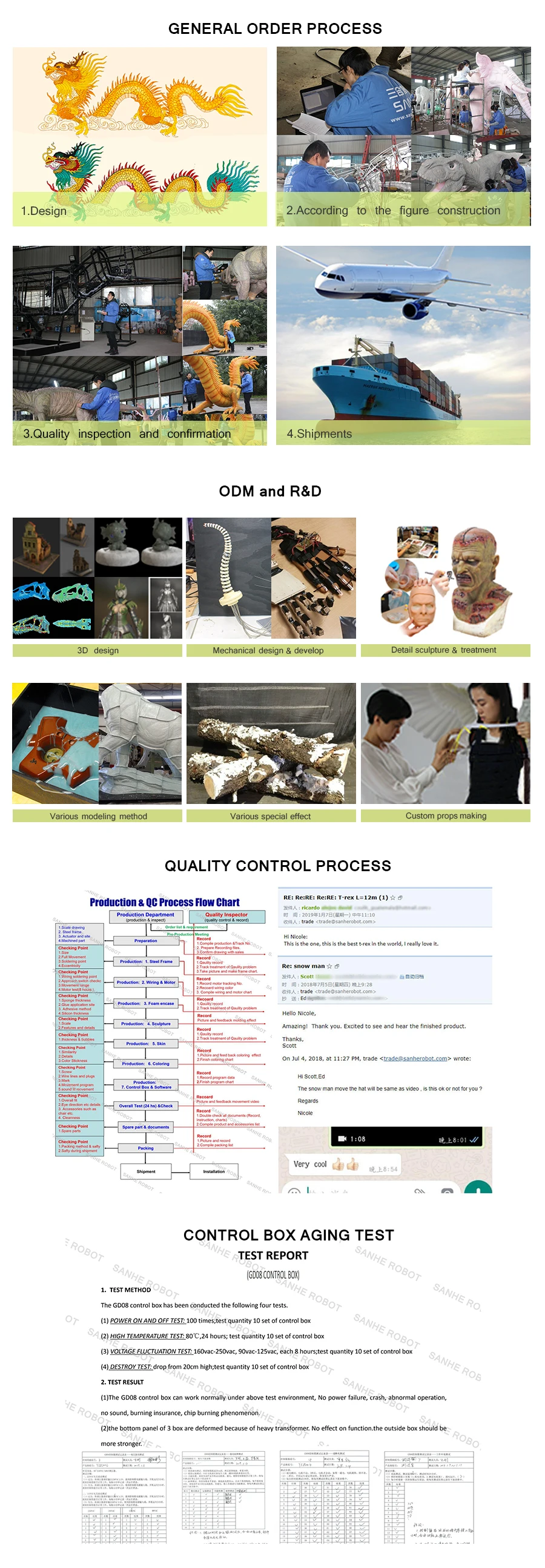
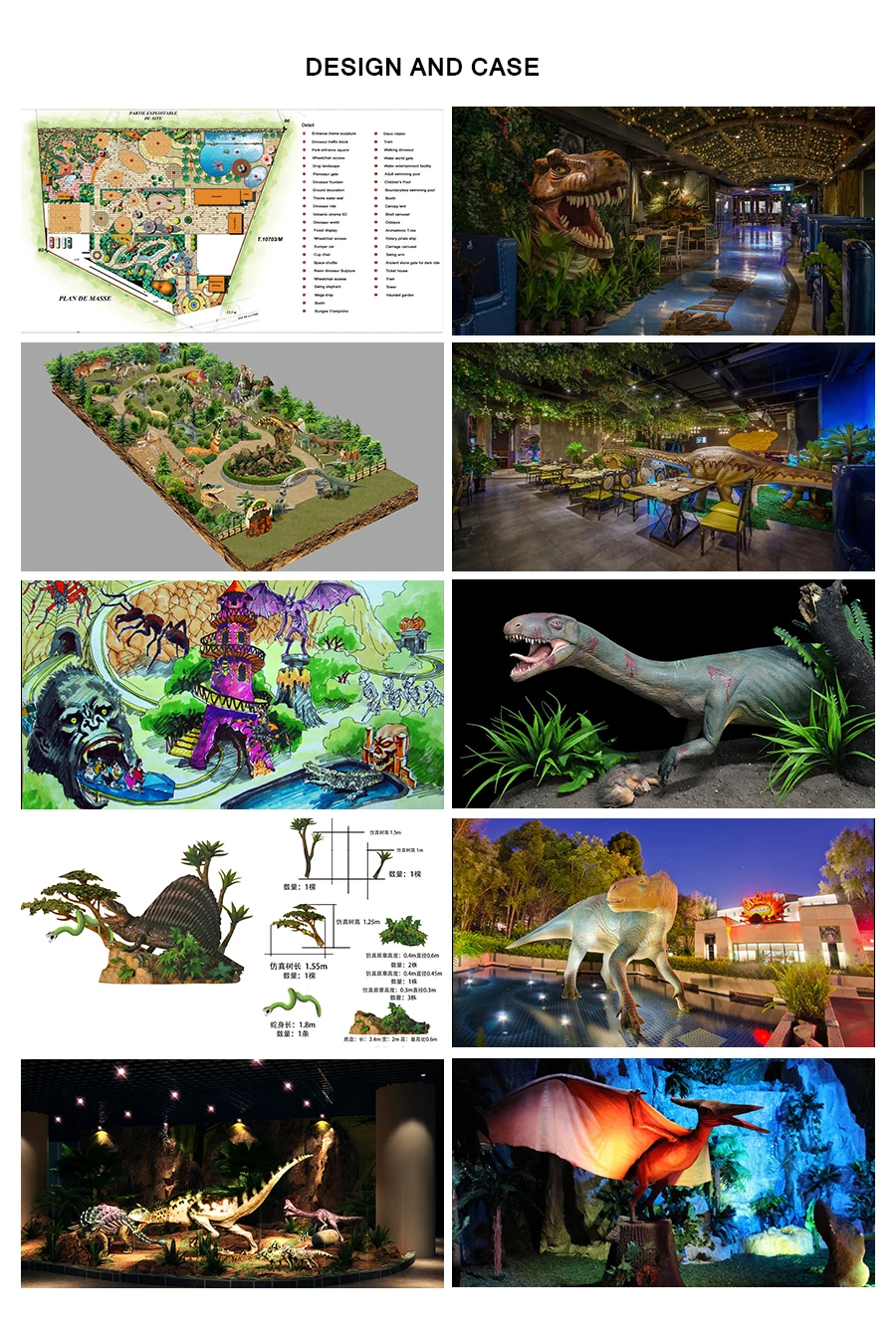
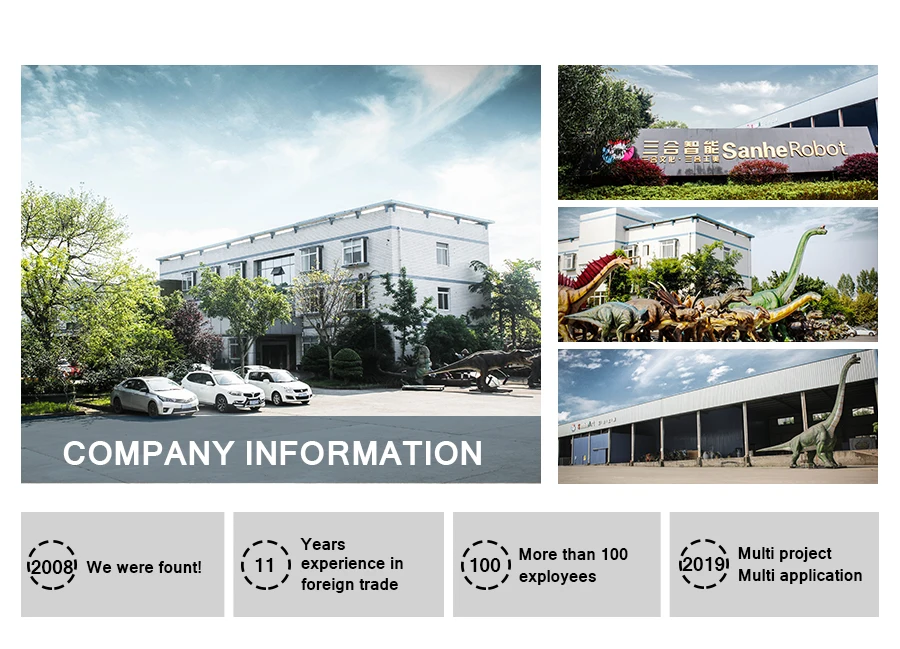
resin statue resin crafts animal crafts cartoon animal model
fiberglass animal sculpture fiberglass decoration from zigong sanhe fiberglass life size rabbit fiberglass cartoon rabbit cute animal amusement park equipment fiberglass theme park decoration simulation life size statues fiberglass statues fiberglass outdoor playground decor playground equipment fiberglass decoration cartoon figure animal sculpture fiberglass cartoon figure fiberglass theme park decoration garden decor fiberglass product resin rabbit sculpture
Fiberglass (American English), or fibreglass (Commonwealth English) is a common type of fiber-reinforced plastic using glass fiber. The fibers may be randomly arranged, flattened into a sheet (called a chopped strand mat), or woven into glass cloth. The plastic matrix may be a thermoset polymer matrix—most often based on thermosetting polymers such as epoxy, polyester resin, or vinyl ester resin—or a thermoplastic.
Cheaper and more flexible than carbon fiber, it is stronger than many metals by weight, is non-magnetic, non-conductive, transparent to electromagnetic radiation, can be molded into complex shapes, and is chemically inert under many circumstances. Applications include aircraft, boats, automobiles, bath tubs and enclosures, swimming pools, hot tubs, septic tanks, water tanks, roofing, pipes, cladding, orthopedic casts, surfboards, and external door skins.
Other common names for fiberglass are glass-reinforced plastic (GRP), glass-fiber reinforced plastic (GFRP) or GFK (from German: Glasfaserverst?rkter Kunststoff). Because glass fiber itself is sometimes referred to as "fiberglass", the composite is also called fiberglass-reinforced plastic (FRP). This article will adopt the convention that "fiberglass" refers to the complete fiber-reinforced composite material, rather than only to the glass fiber within it.
The fiberglass mold process begins with an object known as the plug or buck. This is an exact representation of the object to be made. The plug can be made from a variety of materials, usually certain types of foam.
After the plug has been formed, it is sprayed with a mold release agent. The release agent will allow the mold to be separated from the plug once it is finished. The mold release agent is a special wax, and/or PVA (Polyvinyl alcohol). Polyvinyl alcohol, however, is said to have negative effects on the final mold's surface finish.
Once the plug has its release agent applied, gelcoat is applied with a roller, brush or specially-designed spray gun. The gelcoat is pigmented resin, and gives the mold surface a harder, more durable finish.
Once the release agent and gelcoat are applied, layers of fiberglass and resin are laid-up onto the surface. The fiberglass used will typically be identical to that which will be used in the final product.
In the laying-up process, a layer of fiberglass mat is applied, and resin is applied over it. A special roller is then used to remove air bubbles. Air bubbles, if left in the curing resin, would significantly reduce the strength of the finished mold. The fiberglass spray lay-up process is also used to produce molds, and can provide good filling of corners and cavities where a glass mat or weave may prove to be too stiff.
Once the final layers of fiberglass are applied to the mold, the resin is allowed to set up and cure. Wedges are then driven between the plug and the mold in order to separate the two.
Advanced techniques such as resin transfer molding are also used.